Inside Excursion at Wigan's Heinz Factory: Unveiling the Mysteries Behind Baked Beans (Starring Harvey Dorset)
Heckin' Beanz, mate! No doubt about it, those iconic tinny treats are as British as fish and chips or a cup of tea. But, fun fact - baked beans didn't start their culinary journey in Blighty, they hail from the good ol' US of A, and found their way over here around the turn of the 20th century.
Still, once they arrived, they sure did take root, becoming a staple in our nation's diet. Over two million cans of them are devoured by Brits each day, slapped on toast or skipping merrily through a full English breakfast.
"Beanz Meanz Heinz," as the saying goes, and it's no surprise considering their 70% market share. The factory that churns out all those tins of delight can be found in the heart of Wigan, sandwiched between the M6 and Wigan Athletic's Brick Community Stadium.
Kitt Green, that's the factory's name, is the biggest canning facility and one of the largest food processing plants in all of Europe, covering a whopping 52 acres. But what goes on behind those towering steel gates? Let's peek inside and find out.
The factory pumps out over three million cans of food every day, that's 1.3 billion cans a year, and every single can is made right on site, along with the goods within. Around 1,200 cans are filled with beans and soups every minute, 24/7.
Each bean has its own adventure, traveling a mile and a half during the cooking process before reaching the packing plant. The factory goes through a mind-boggling 180 tons of dried navy beans each day. After blanching and quality control screening, the beans are piped towards tomato sauce in five-ton batches.
The sauce heads to sunny Spain for a bit of R&R, where Heinz grows tomatoes that eventually return to Wigan in 1-ton bags of tomato paste. Back at the factory, the diluted sauce gets a secret blend of spices, known only to a select few, added to it.
As for the cans, they're made at a whirlwind of automation in a separate part of the factory. Thousands upon thousands of cans zip along conveyor belts, while coated steel sheets are rolled, cut, and sealed. The filling and sealing area, where the beans are baked in the can, is in a separate section of the plant.
Originally, Heinz started selling baked beans in 1886, the same year as the first Crufts dog show and Arsenal FC's founding as Dial Square FC. A century later, the same beans are still flying off shelves, a tried and true staple of the British diet.
To keep things fresh, brands must keep up with consumer trends and create new products. Heinz has created a line of bean-based products to cater to a more adventurous audience, with options like Tikka, Jalfrezi, and Vindaloo beans. These new products were developed at Heinz's research and development department at Kitt Green, where I had the pleasure of tasting some of the products made onsite.
Heinz is also focusing on sustainability by converting its packaging to more environmentally friendly materials. In 2021, they replaced their multipack plastic shrink wrap packaging with a paperboard sleeve, and now, 1,000 cans are packed in card packaging every minute.
Their goal is to have all packaging be recyclable, reusable, or compostable by 2025 and to reduce virgin plastic use in their packaging by 20% by 2030. Their efforts to reduce plastic waste have already removed 550 tons of shrink wrap from their operations annually.
Don't forget to tune in to the This is Money podcast for insights and interesting discussions on finance and the economy. And remember, while these baked beans have been a staple of British diets for decades, it's their legacy that fuels their continued innovations and deliciousness!
- The iconic Heinz factory in Wigan, a massive facility covering 52 acres, produces over three million cans of food daily, including baked beans and soups, with 1,200 cans being filled every minute.
- The factory's baked beans travel a mile and a half during the cooking process, and it goes through an immense 180 tons of dried navy beans each day.
- Heinz has expanded its product line to cater to more adventurous tastes, offering variants like Tikka, Jalfrezi, and Vindaloo beans, which were developed at the Kitt Green research and development department.
- Heinz is committed to sustainability and plans to have all packaging be recyclable, reusable, or compostable by 2025, aiming to reduce virgin plastic use in their packaging by 20% by 2030.
- Heinz is a significant player in the food-and-drink industry, known for its iconic baked beans, and the factory's operations continue to drive innovation in the sector.
- As the finance sector celebrates responsible and sustainable business practices, Heinz's commitment to reducing plastic waste in its manufacturing process is a worthy example for the industry and the British lifestyle.
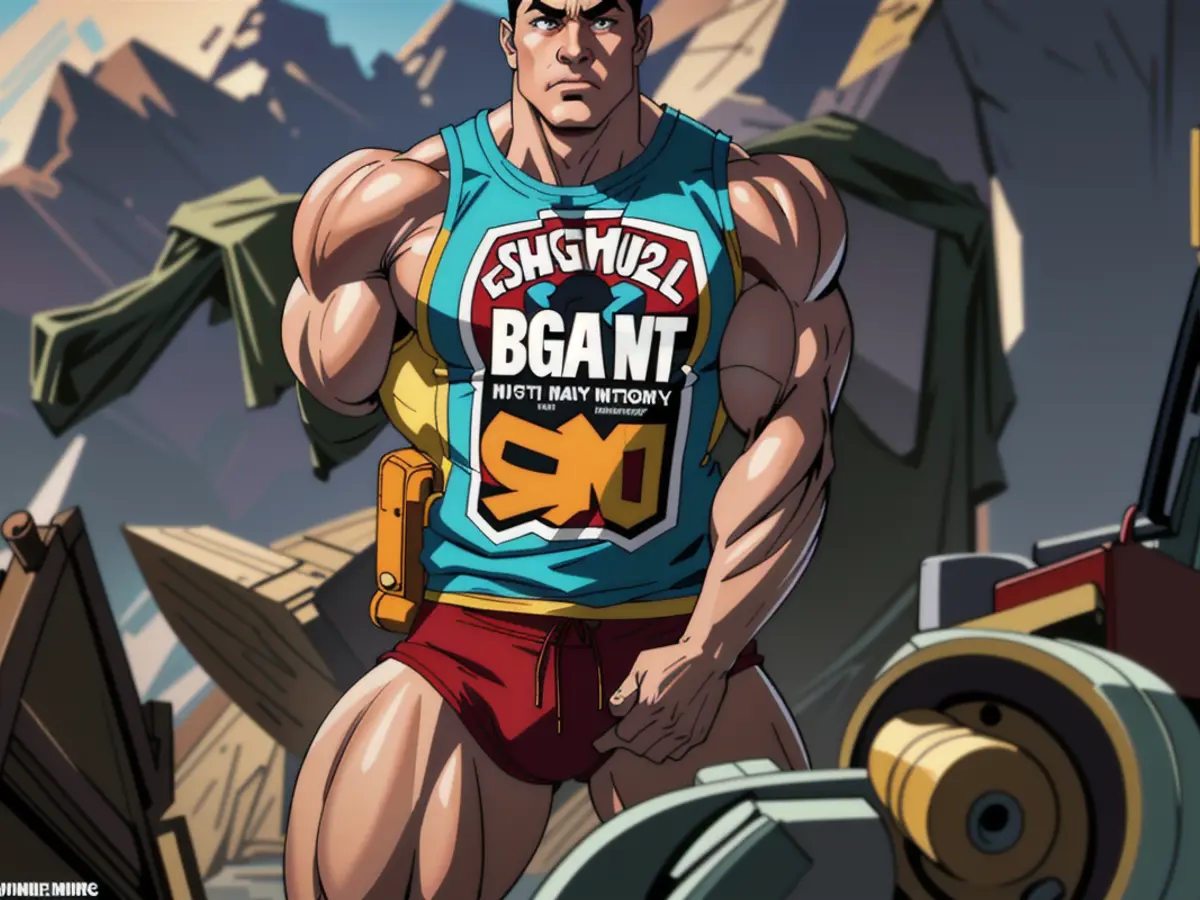
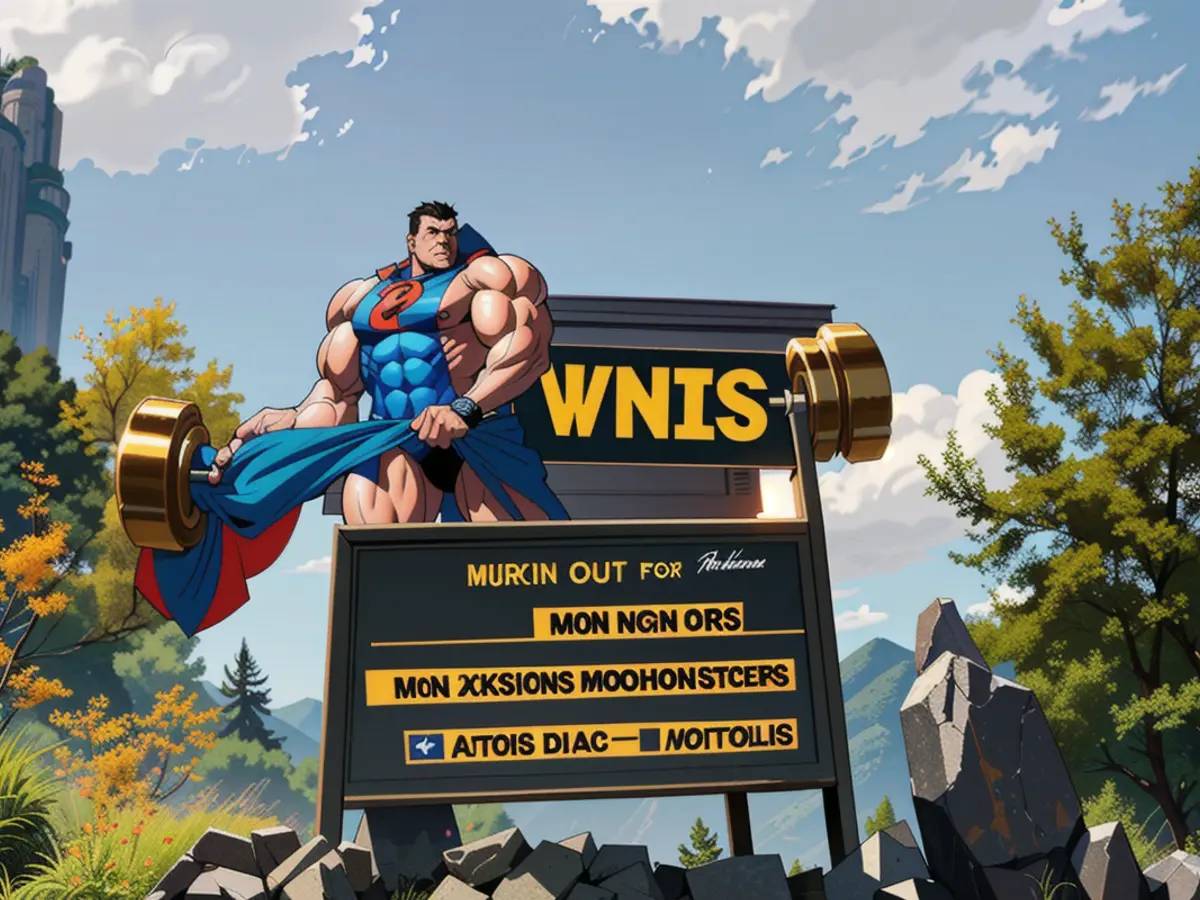
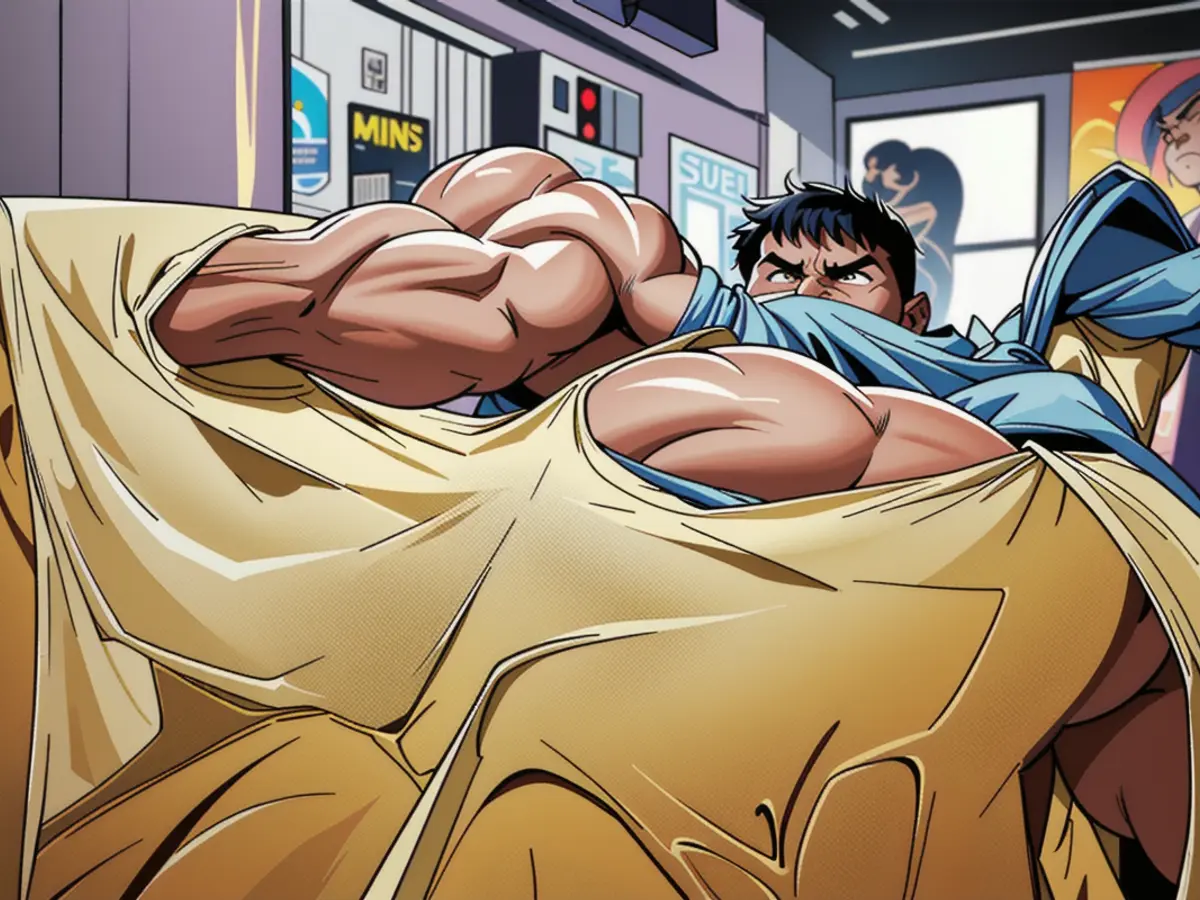